One Of The Best Tips About What Are The Benefits Of Mechanical Splicing

Mechanical Splicing
1. What's the Big Deal with Mechanical Splicing?
Okay, let's talk fiber optics. Connecting those tiny strands can feel like performing surgery with oven mitts, right? Traditionally, you'd think of fusion splicing — melting the fibers together. But there's another way, a method that might just make your life a whole lot easier: mechanical splicing. Think of it like using tiny, super-precise clamps to hold the fibers together. Sounds straightforward, doesn't it?
Mechanical splicing is essentially a process where you align two optical fibers and hold them together with a mechanical fixture. No heat, no fancy fusion equipment, just good old-fashioned precision. This method relies on accurately aligning the fiber cores so that light can pass from one fiber to the other with minimal loss. Its like making sure two train tracks line up perfectly so the train doesnt derail... except much, much smaller, and with light instead of trains.
Now, why should you even care? Well, consider the situations where speed and simplicity are crucial. Imagine a quick repair needed in the field, or a temporary connection for testing purposes. That's where mechanical splicing truly shines. It's the duct tape of the fiber optic world, only significantly more sophisticated and effective.
We'll delve into the real meat of why mechanical splicing is such a useful technique. From cost savings to portability, there's a whole host of reasons you might choose this method over fusion splicing. So stick around, and let's unpack the benefits, one by one. No need to be intimidated by fiber optics; we'll keep it light (pun intended!).
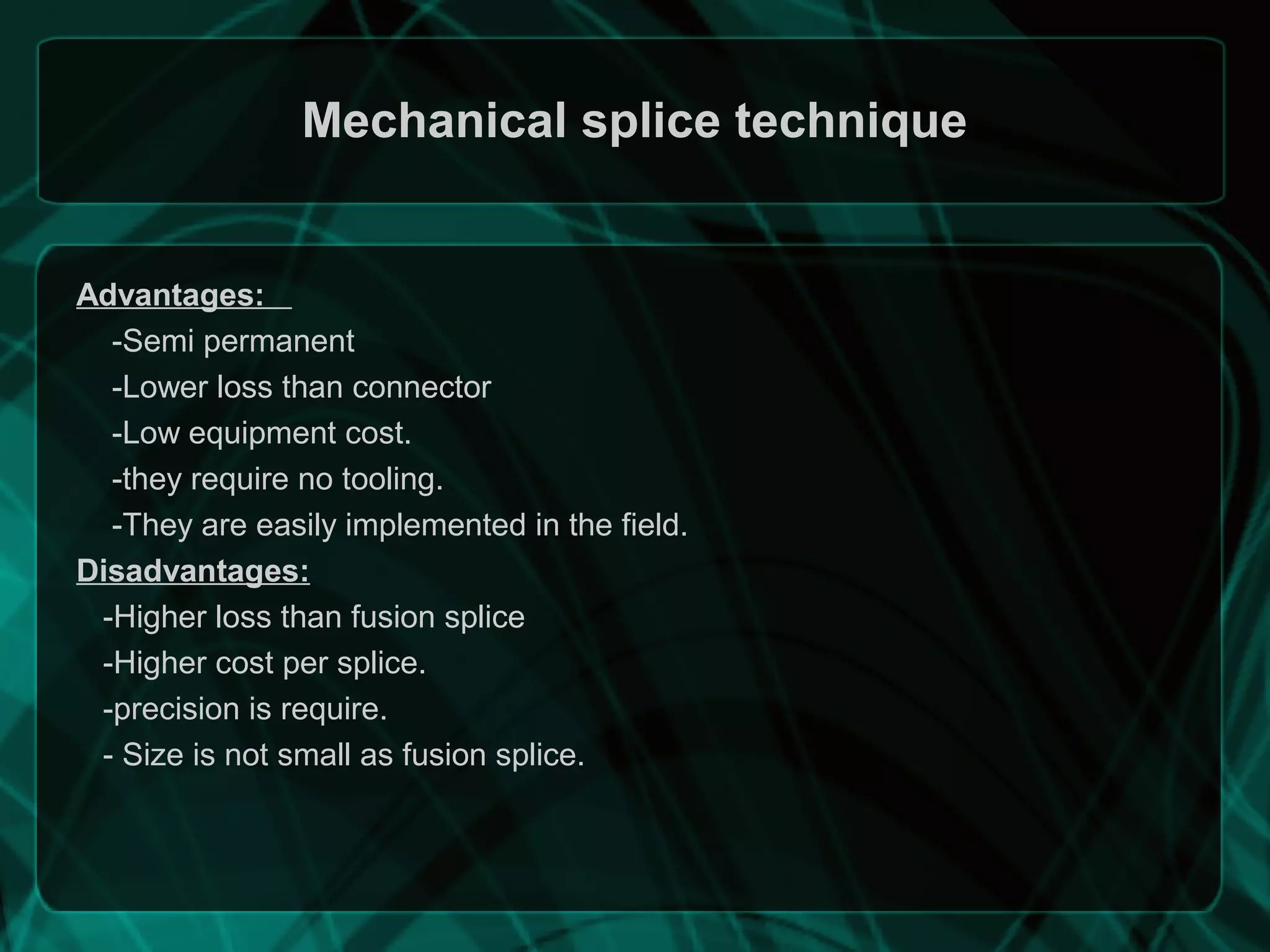
Mechanical Splicing Techniques For Optical Fiber PPT
The Top Benefits of Mechanical Splicing
2. Saving Time and Money
One of the biggest advantages of mechanical splicing is the reduced upfront cost. Fusion splicers are expensive pieces of equipment, requiring significant investment and ongoing maintenance. Mechanical splicing, on the other hand, relies on relatively inexpensive tools and connectors. It's like the difference between buying a fancy espresso machine and just using a French press; both get the job done, but one requires a far bigger financial commitment.
Time is also a major factor. Fusion splicing takes time. You've got to prepare the fibers, align them perfectly, and then wait for the fusion process to complete. Mechanical splicing cuts down on this significantly. With a little practice, you can make a connection in just a few minutes, making it ideal for situations where speed is of the essence. Think of it as the difference between cooking a gourmet meal from scratch and throwing something quick and easy in the microwave.
And because mechanical splicing is quicker and doesn't require specialized training to the same degree as fusion splicing, labor costs can also be lower. You don't need a highly skilled technician to perform a basic mechanical splice, freeing up your experienced personnel for more complex tasks. It's all about efficiency!
Ultimately, the cost and time savings associated with mechanical splicing can make a significant impact on your project's bottom line. Especially for small-scale projects or emergency repairs, the benefits are undeniable. Of course, the choice depends on the specific application, but keep these factors in mind when weighing your options.
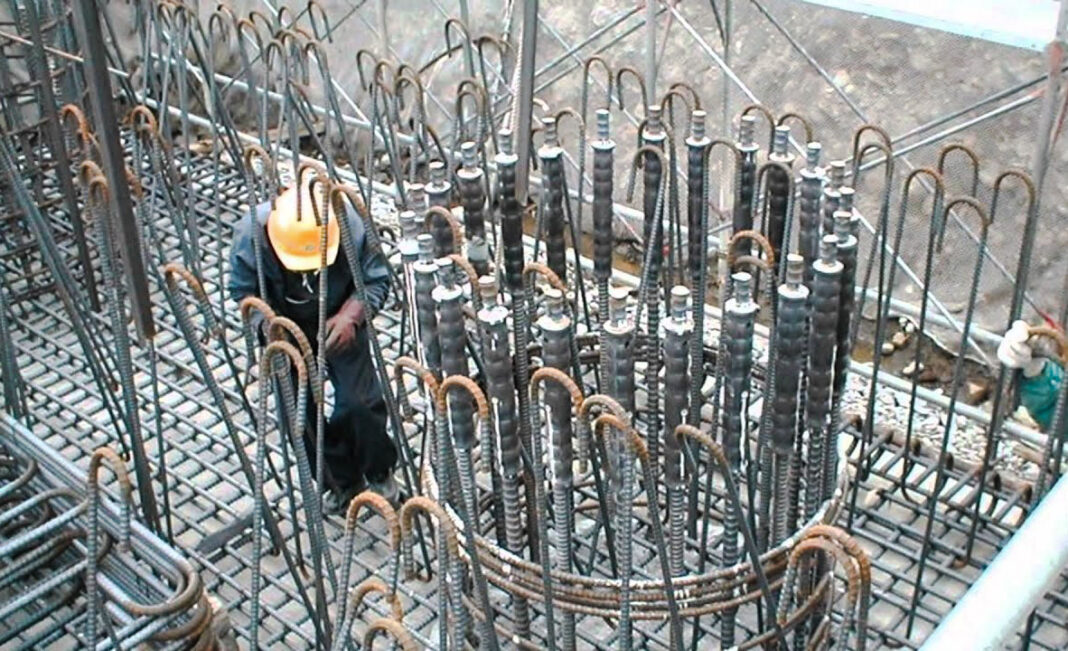
Advantages And Types Of Mechanical Splices For Concrete Rebar
Portability and Ease of Use
3. Making Connections on the Go
Imagine you're working on a fiber optic network in a remote location, miles from the nearest power outlet. Dragging a bulky fusion splicer around isn't exactly practical, is it? This is where the portability of mechanical splicing really shines. The tools needed are compact and lightweight, making them easy to transport and use in the field. It's like comparing a desktop computer to a laptop; both have their uses, but one is far more convenient for working on the move.
The simplicity of the process also contributes to its ease of use. You don't need extensive training or a deep understanding of fiber optic theory to perform a mechanical splice. With a little practice and the right tools, just about anyone can learn to make a reliable connection. That makes it ideal for situations where you need to empower a wider range of personnel to handle basic fiber optic tasks.
This ease of use also translates to faster deployment times. In emergency situations, such as a damaged fiber optic cable, the ability to quickly restore service is crucial. Mechanical splicing allows you to do just that, minimizing downtime and keeping your network running smoothly. Think of it as having a reliable backup plan when things go wrong.
Furthermore, consider temporary installations or testing environments. Mechanical splicing provides a flexible and convenient way to connect fibers for short periods of time, without the commitment or expense of a permanent fusion splice. This makes it a valuable tool for engineers and technicians who need to experiment and troubleshoot fiber optic systems.
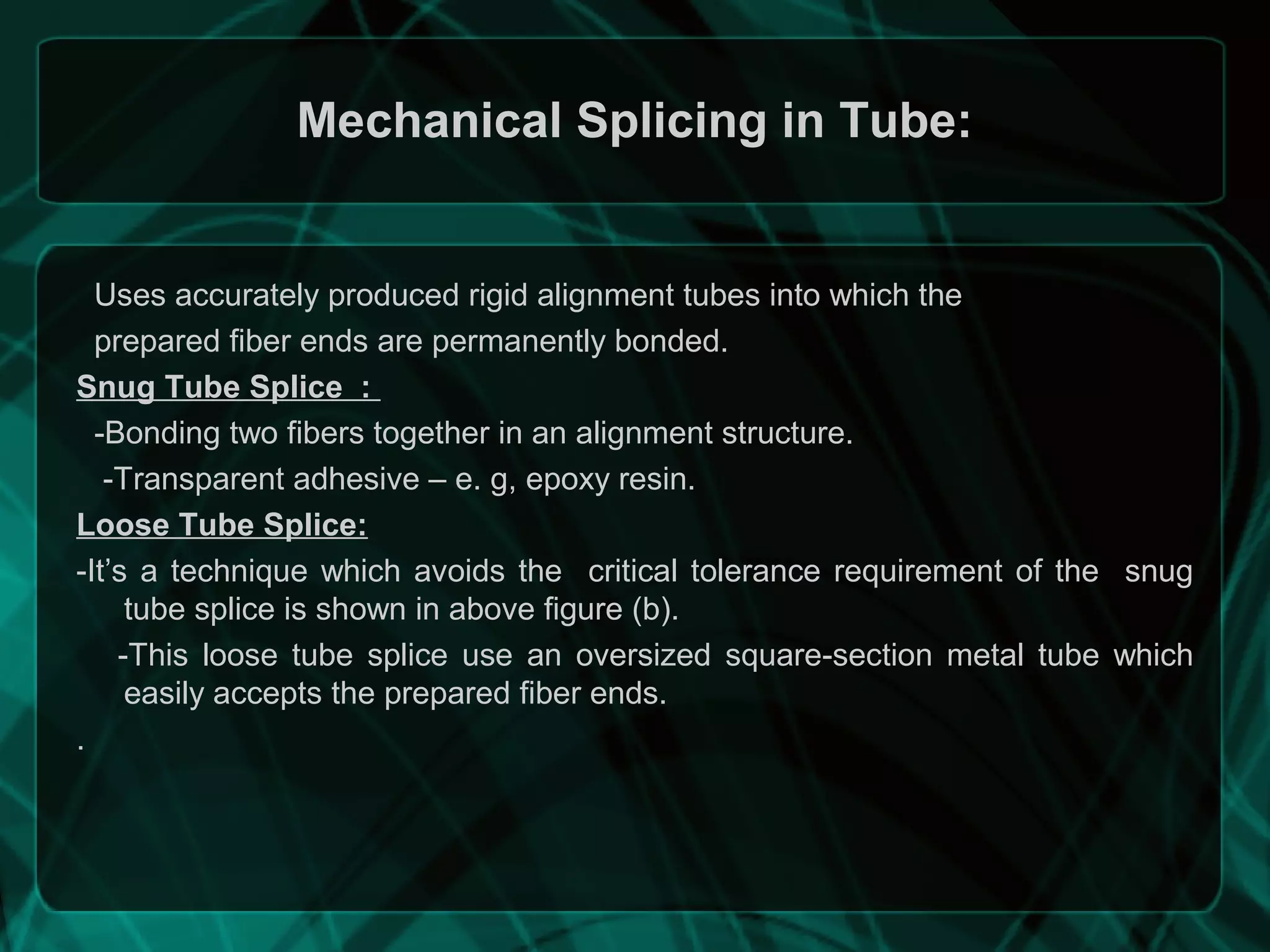
When Mechanical Splicing is Your Best Bet
4. Know When to Fold 'Em, Know When to Splice 'Em
Alright, so we've sung the praises of mechanical splicing. But when exactly is it the right choice? Well, it's not a one-size-fits-all solution. Mechanical splicing excels in situations where you need quick repairs, temporary connections, or cost-effective solutions for smaller projects. It's like having a Swiss Army knife; it's not always the best tool for every job, but it's incredibly versatile and convenient.
Think about scenarios where you're dealing with a limited number of fibers. If you only need to connect a few fibers, the cost and complexity of fusion splicing might not be justified. Mechanical splicing provides a simpler, more affordable alternative. It's also great for situations where you're working in tight spaces or challenging environments where maneuvering a fusion splicer would be difficult.
Emergency restoration is another area where mechanical splicing shines. When a fiber optic cable is damaged, time is of the essence. Mechanical splicing allows you to quickly restore service, minimizing downtime and preventing costly disruptions. It's like having a spare tire for your network; it might not be as good as the original, but it'll get you back on the road.
However, it's important to acknowledge the limitations of mechanical splicing. While it's generally reliable, the insertion loss (the amount of light lost at the connection) is typically higher than with fusion splicing. This means it might not be the best choice for long-distance, high-bandwidth applications where signal integrity is paramount. So, before you reach for the mechanical splice, consider the specific requirements of your project.
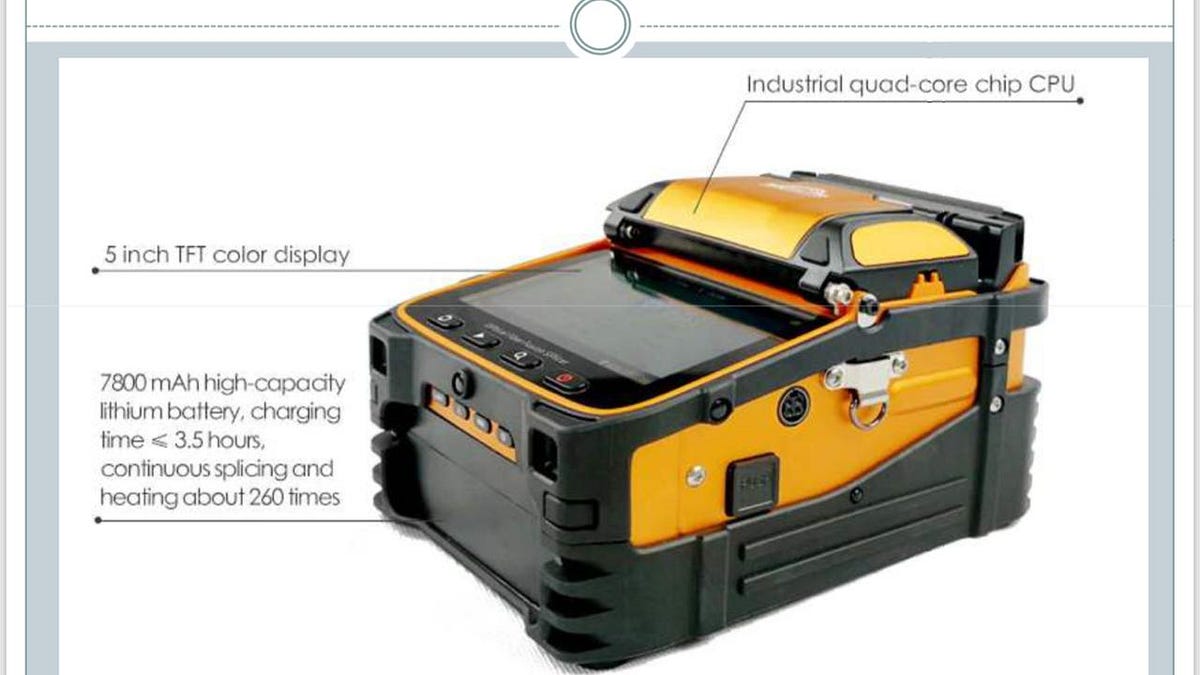
The Benefits Of Using A Fusion Splicing Machine Comprehensive Guide
Potential Drawbacks and Considerations
5. Not a Perfect Solution, But a Great Option
Let's be real, mechanical splicing isn't perfect. While it offers many benefits, it's important to be aware of its limitations. One of the main concerns is the higher insertion loss compared to fusion splicing. This means that more light is lost at the connection, which can impact signal quality, especially over long distances. It's like having a slightly leaky pipe; you're still getting water, but some is being lost along the way.
Another consideration is the long-term reliability of mechanical splices. While they can provide a stable connection, they are more susceptible to environmental factors such as temperature changes and humidity. Over time, this can lead to degradation of the connection and increased insertion loss. It's like comparing a glued joint to a welded joint; the weld is generally stronger and more durable.
Furthermore, the precision required for mechanical splicing can be challenging, especially for those who are new to the process. Proper fiber preparation and alignment are crucial for achieving a low-loss connection. A slight misalignment can significantly increase the insertion loss and negatively impact performance. It's like trying to assemble a puzzle with pieces that don't quite fit; you can force them together, but the result won't be pretty.
Finally, it's essential to use high-quality mechanical splice connectors from reputable manufacturers. Cheap, poorly made connectors can lead to unreliable connections and increased insertion loss. It's like buying a generic phone charger; it might work for a while, but it's likely to fail sooner than a charger from a trusted brand. So, when it comes to mechanical splicing, investing in quality is definitely worth it.

Fiber Optic Connectors, Splices, And Tools Ppt Download
FAQ
6. Your Burning Questions Answered
Still got questions about mechanical splicing? Don't worry, you're not alone! Here are a few of the most common questions we get asked:
Q: Is mechanical splicing permanent?A: Not necessarily. While a mechanical splice can be quite reliable, it's often considered semi-permanent. They are typically used for emergency repairs or temporary setups, whereas fusion splices provide more permanent connections. You can leave them in place for the long term, but it's generally recommended to monitor them and consider a fusion splice if absolute reliability is paramount.
Q: How much insertion loss can I expect with a mechanical splice?A: Insertion loss varies depending on the quality of the connectors and the precision of the splice. Typically, you can expect insertion loss to be around 0.1 to 0.5 dB. This is higher than fusion splicing, which typically has insertion loss below 0.1 dB. Check the manufacturer's specifications for the exact insertion loss of the connectors you are using.
Q: Can I use mechanical splicing on all types of fiber?A: Yes, mechanical splicing can be used on most common types of optical fiber, including single-mode and multimode fibers. However, it's important to select connectors that are specifically designed for the type of fiber you are using. Using the wrong connector can result in poor performance and increased insertion loss.
Q: What tools are needed for mechanical splicing?A: You'll typically need a fiber cleaver to create clean, flat fiber ends, a fiber stripper to remove the protective coating, a cleaning tool to remove any debris, and the mechanical splice connectors themselves. Some kits come with all these tools included, which can be a convenient option. And of course, you'll need a visual fault locator (VFL) to test the connection afterwards. Think of it as the basic toolkit for a fiber optic handyman!