Outrageous Tips About What Are The Disadvantages Of A Torque Sensor

Torque Sensor Vs Cadence
Understanding Torque Sensors
1. Cost Considerations
Alright, let's talk torque sensors. They're pretty amazing pieces of tech, crucial in everything from your car's engine management to robotic arms in factories. But, like that fancy coffee maker you splurged on, they come with a few downsides. The biggest one? The initial investment. High-precision torque sensors, especially those with advanced features, can seriously dent your budget. Think of it as needing to buy premium gasoline for a high-performance engine; the performance gain comes at a price.
The cost isn't just about the sensor itself. Factor in the installation expenses. Depending on the application, you might need specialized equipment or a skilled technician to integrate the sensor correctly. It's not always a simple plug-and-play situation, you know? Plus, don't forget about calibration costs. Regular calibration is essential to maintain accuracy, and those calibration services can add up over time. Suddenly, that "small" investment seems a bit larger, doesn't it?
And then, there's the potential for replacement. Nothing lasts forever, especially in harsh industrial environments. Torque sensors, despite their ruggedness, can fail due to wear and tear, overloading, or environmental factors. So, consider the long-term cost of ownership, including potential replacements and repairs. It's like owning a vintage car; the upfront cost might be tempting, but the maintenance can be a real headache.
Basically, while torque sensors provide valuable data, be prepared to open your wallet a bit wider than you might initially expect. It's a balancing act between the benefits you'll gain and the money you'll spend. Is the added precision and control worth the higher price tag? Thats the question to ask.
2. Environmental Sensitivity
Torque sensors aren't always the toughest cookies in the jar. Many types can be quite sensitive to their surroundings. Temperature changes, for example, can wreak havoc on their accuracy. Imagine trying to bake a cake when your oven keeps fluctuating by 50 degrees! The readings can drift, leading to inaccurate data and potentially messing up whatever system relies on that information. Thats why they frequently need temperature compensation built into the design.
Then theres the issue of electromagnetic interference (EMI). In electrically noisy environments, like near powerful motors or transformers, the sensors signal can get garbled. Its like trying to have a phone conversation during a rock concert; you can barely hear a thing! Shielding and proper grounding are often necessary to mitigate EMI, adding complexity and potentially cost to the installation.
Vibration is another enemy. Excessive vibration can cause the sensor to malfunction or even fail prematurely. Think of it as shaking a soda can before opening it; things are bound to go wrong. Depending on the application, you might need to use vibration dampeners or isolation mounts to protect the sensor.
Humidity and dust can also cause problems, especially for sensors that aren't properly sealed. Moisture can corrode internal components, while dust can clog sensitive areas. Regular cleaning and maintenance are essential to keep the sensor functioning correctly in these conditions. So, before you drop one into a swamp cooler, double-check its specs!
3. Calibration and Maintenance
4. Calibration and Maintenance
Like a finely tuned instrument, a torque sensor needs regular calibration to ensure it's providing accurate readings. Without calibration, the data it provides can become unreliable, leading to faulty decisions and potentially damaging equipment. Think of it as using a ruler that's been stretched; you'll never get an accurate measurement!
The frequency of calibration depends on the application and the sensor's specifications. High-precision applications, such as aerospace or medical equipment, might require calibration more frequently than less demanding applications, like industrial mixing. It's like getting your car serviced; the more you drive it, the more often it needs maintenance.
Calibration isn't always a simple DIY task. It often requires specialized equipment and trained technicians. Sending the sensor to a calibration lab can be costly and time-consuming. However, neglecting calibration can be even more costly in the long run, as it can lead to inaccurate data and potentially dangerous situations.
Beyond calibration, regular maintenance is essential to keep the sensor functioning properly. This includes cleaning the sensor, checking for loose connections, and inspecting for any signs of damage. Proper maintenance can extend the sensor's lifespan and prevent costly repairs or replacements. Treat it well and it will treat you well, right?
5. Complexity of Integration
Integrating a torque sensor into a system isn't always a walk in the park. Depending on the application, it can require a significant amount of engineering effort. You need to carefully consider the sensor's mounting location, wiring, and communication protocol. It's not just about slapping it on and hoping for the best!
The mechanical integration can be particularly challenging. You need to ensure that the sensor is properly aligned and secured to the equipment. Any misalignment or looseness can introduce errors in the readings. Think of it as trying to balance a wobbly table; it's going to throw everything off. Also, ensure you are not applying torque to the body of the sensor or damage can occur.
The electrical integration can also be tricky. You need to choose the right wiring and communication protocol to transmit the data to the control system. You also need to protect the sensor from electrical noise and interference. A poorly designed electrical connection can lead to inaccurate readings and system malfunctions. So, take your time and get it right.
And then there's the software integration. You need to write code to read the data from the sensor and interpret it correctly. This can require a deep understanding of the sensor's specifications and the control system's architecture. If you're not comfortable with coding, you might need to hire a software engineer to help you out. Its like translating from a foreign language; you need someone who speaks the language fluently.
6. Limited Lifespan and Potential for Failure
Let's face it: nothing lasts forever, and that includes torque sensors. Despite their robust construction, they are susceptible to wear and tear over time. The constant stress and strain of measuring torque can eventually lead to fatigue and failure. Its like bending a paperclip back and forth; eventually, it's going to snap.
The lifespan of a torque sensor depends on several factors, including the application, the operating conditions, and the sensor's design. High-stress applications, such as those involving repetitive loading or extreme temperatures, can significantly shorten the sensor's lifespan. So, if you're putting it through the wringer, expect it to wear out sooner.
There are several potential failure modes. The sensor's internal components can break down, the wiring can become damaged, or the calibration can drift beyond acceptable limits. Any of these failures can lead to inaccurate readings and system malfunctions. Its like a chain; if one link breaks, the whole thing falls apart.
Regular inspection and maintenance can help to extend the sensor's lifespan and prevent unexpected failures. However, even with the best care, a torque sensor will eventually need to be replaced. It's just a fact of life. So, be prepared for the inevitable and factor in the cost of replacement when evaluating the long-term cost of ownership. Just like tires on your car, they'll eventually need replacing.

FAQ About Torque Sensors
7. Q
A: Calibration frequency depends on the application and the sensor's specifications. High-precision applications may require calibration every few months, while less demanding applications may only need it annually. Always refer to the manufacturer's recommendations.8. Q
A: Yes, temperature changes can significantly affect the accuracy of many torque sensors. Some sensors have built-in temperature compensation, but external compensation may be necessary in extreme conditions.9. Q
A: Common signs include erratic or inconsistent readings, signal drift, and complete signal loss. Physical damage to the sensor or its wiring can also indicate a problem. Also, check that the wiring connections are solid.

Torque Sensor Motor At Natasha Peter Blog
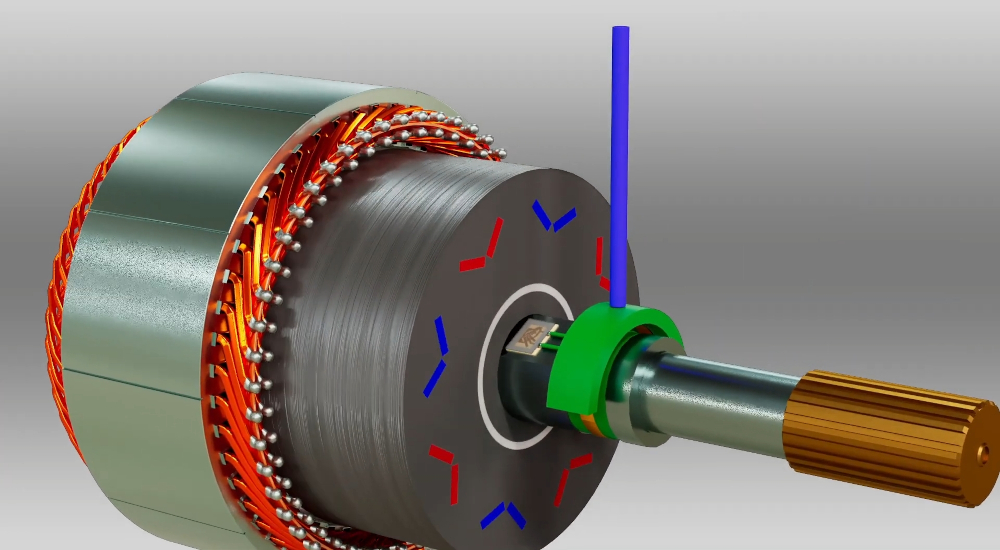
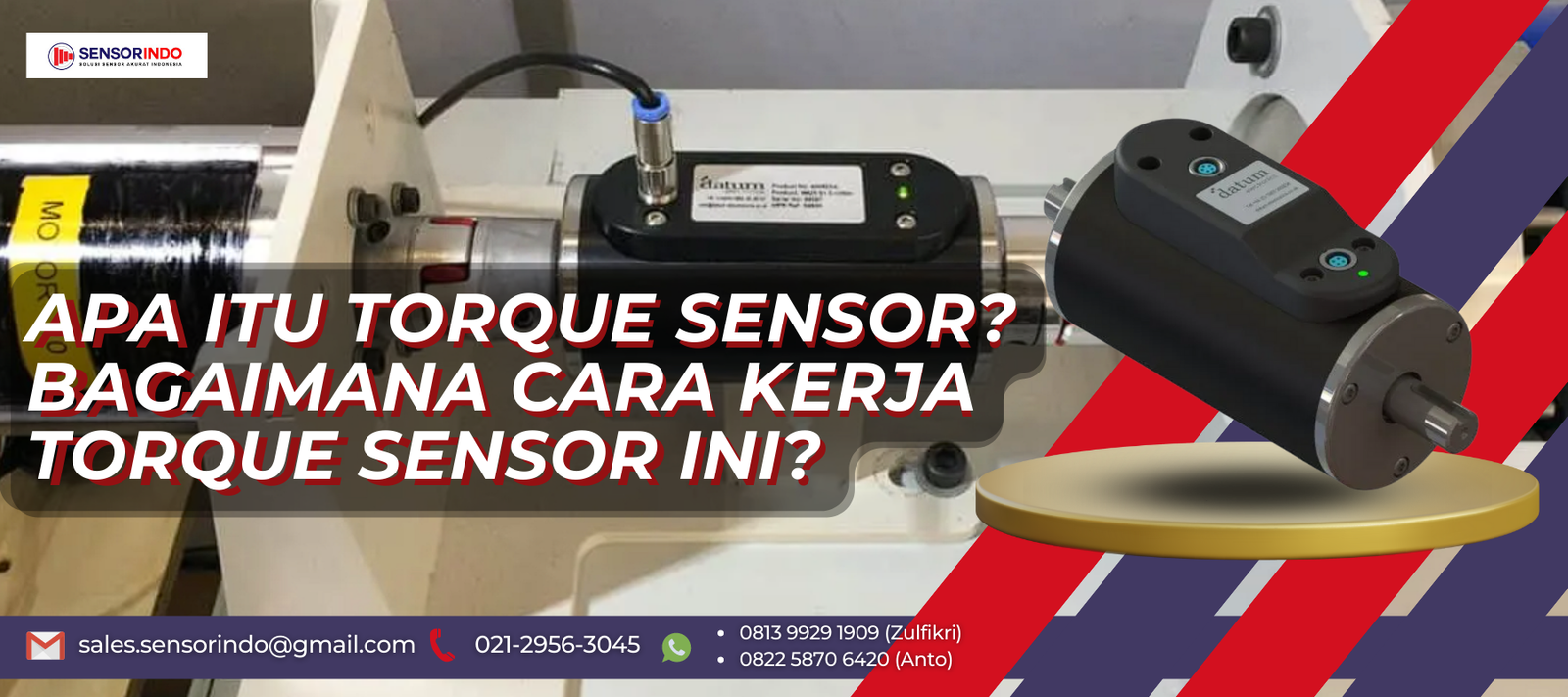
Torque Sensor Problems At Zoe Oatley Blog
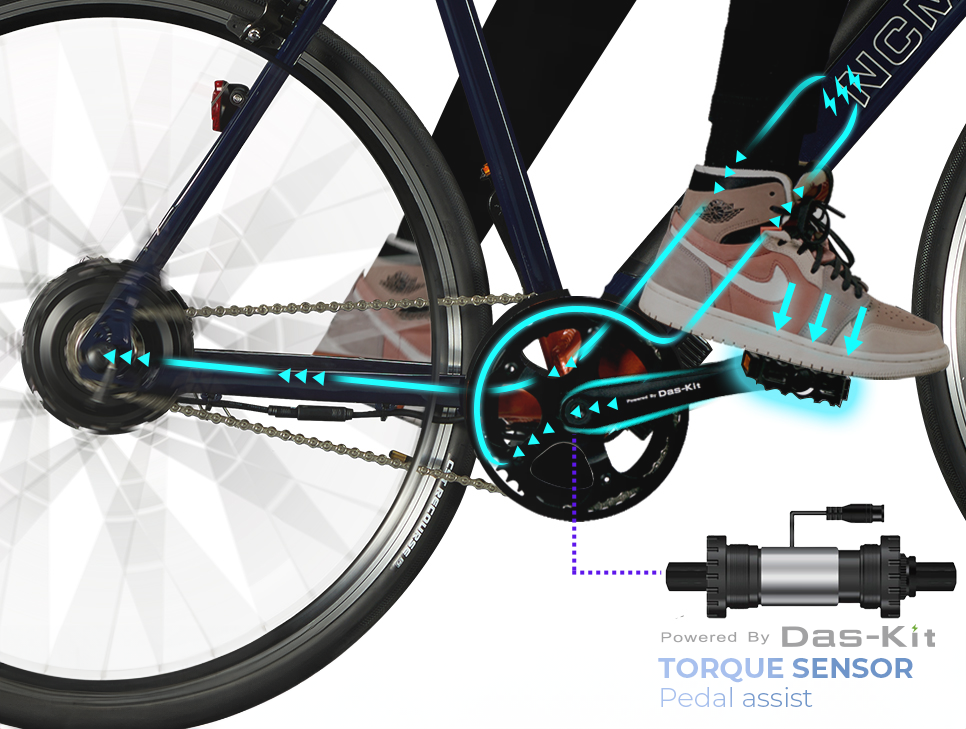