Wonderful Tips About How To Splice Wires With Crimp Connectors

How To Crimp Wire Connectors
Splicing Wires Like a Pro
1. Why Crimp Connectors? Let's Get Real
Let's be honest, dealing with electrical wires can feel a bit like wrestling an octopus. You've got multiple arms (or wires), they're all slippery, and one wrong move could lead to sparks. That's where crimp connectors come in as your trusty sidekick. They offer a relatively easy and secure way to join wires together without needing a soldering iron and a prayer. Think of them as the LEGO bricks of the electrical world — they click together and stay put (when done right, of course!).
These little gadgets are fantastic because they're generally considered safer than just twisting wires together and hoping for the best. Imagine the alternative: a loose connection that overheats and potentially causes a fire. Yikes! Crimp connectors, when properly installed, create a tight, gas-tight seal that prevents corrosion and ensures a reliable electrical connection. That means less hassle and more peace of mind.
Plus, crimp connectors are incredibly versatile. You'll find them in all sorts of applications, from automotive wiring to household electrical repairs. They come in different sizes and types to accommodate various wire gauges, so you can always find the perfect fit for your project. Just make sure you choose the right connector for the job, and you'll be golden.
So, if you're looking for a straightforward and reliable way to splice wires, crimp connectors are definitely worth considering. They're a game-changer for both DIY enthusiasts and professional electricians alike. Now, let's dive into the specifics of how to use them properly.
2. Tools of the Trade
Before you even think about touching those wires, you'll need to assemble your toolkit. Think of it like preparing for battle, but instead of swords and shields, you've got crimpers and wire strippers. First and foremost, you absolutely need a good quality crimping tool. Don't skimp on this — a cheap crimper can lead to loose connections and a whole lot of frustration. Invest in a decent one, and it'll last you for years.
Next up, you'll need a wire stripper. This tool is essential for removing the insulation from the wires without damaging the copper strands inside. Using a knife or scissors is a big no-no; you'll likely nick the wire, which weakens it and can lead to problems down the line. A wire stripper provides a clean, precise cut every time.
Of course, you'll also need the crimp connectors themselves. As mentioned earlier, they come in different sizes and types, so make sure you choose the right ones for the gauge of wire you're working with. Color-coded connectors can be helpful, as they often indicate the wire size range they're designed for. For example, red connectors are typically for smaller wires, while blue and yellow connectors are for larger ones. And don't forget safety glasses! Protecting your eyes is always a good idea when working with electricity.
Finally, a multimeter can be useful for testing the connection after you've made the splice. This will help you ensure that the wires are properly connected and that there's continuity. Better safe than sorry, right? With these tools in hand, you'll be well-equipped to tackle any wiring project with confidence.
3. The Step-by-Step Guide
Alright, let's get down to the nitty-gritty (oops, almost slipped up there!). Actually, lets get down to business! The first step is to prepare the wires. Use your wire stripper to carefully remove about 1/2 inch of insulation from the end of each wire you want to splice. Make sure you don't nick the copper strands inside. A clean cut is key for a solid connection.
Next, twist the exposed strands of each wire together to create a neat, compact bundle. This will ensure that all the strands make good contact with the crimp connector. Now, insert the twisted ends of both wires into the crimp connector. Make sure the wires are fully inserted and that the insulation is butted up against the connector body. This will prevent moisture from getting into the connection.
Once the wires are in place, grab your crimping tool and position the connector in the appropriate crimping jaw. Apply firm, even pressure until the crimper releases. You should feel a distinct click or ratcheting action, indicating that the connection is properly crimped. Don't over-crimp, as this can damage the connector and weaken the connection.
Finally, give the wires a gentle tug to make sure they're securely held in place. If the wires pull out easily, the connection is not properly crimped, and you'll need to start over with a new connector. If the wires are secure, you're good to go! You can now insulate the connection with electrical tape or heat-shrink tubing for added protection.
4. Troubleshooting Tips
Even with the best intentions, things can sometimes go awry. One common problem is a loose connection. This can happen if the crimp connector is not properly sized for the wire gauge, or if the crimping tool is not adjusted correctly. Always double-check that you're using the right connector and that your crimper is in good working order.
Another issue can be damaged wires. If you accidentally nicked the wires while stripping the insulation, the connection may be weak or unreliable. In this case, it's best to cut off the damaged section of wire and start over with a fresh piece. It's better to be safe than sorry when it comes to electrical connections.
Sometimes, the crimp connector itself can be faulty. If you notice any cracks, corrosion, or other damage to the connector, don't use it. A faulty connector can lead to a poor connection and potentially dangerous situation. Always inspect your connectors before using them.
If you're still having trouble, don't hesitate to consult a qualified electrician. Electrical work can be dangerous, and it's always best to seek professional help if you're unsure about anything. Remember, safety first!
5. Beyond the Basics
Once you've mastered the basics of splicing wires with crimp connectors, you can start exploring more advanced techniques. One useful trick is to use heat-shrink crimp connectors. These connectors have a heat-shrink sleeve that shrinks down when heated, providing an extra layer of insulation and protection against moisture and corrosion.
Another advanced technique is to use crimp connectors with built-in strain relief. These connectors have a feature that prevents the wires from being pulled out of the connection, which can be especially useful in applications where the wires are subject to vibration or movement. Imagine the wires on a car stereo or engine; extra strain relief can prevent constant repairs.
You can also use crimp connectors to create custom wire harnesses. This involves connecting multiple wires together in a specific configuration. Wire harnesses are commonly used in automotive, aerospace, and industrial applications. By using crimp connectors, you can create a reliable and organized wire harness that meets your specific needs.
Finally, don't be afraid to experiment and try different types of crimp connectors to find what works best for you. There are many different options available, each with its own advantages and disadvantages. With a little practice and experimentation, you'll become a crimp connector expert in no time!
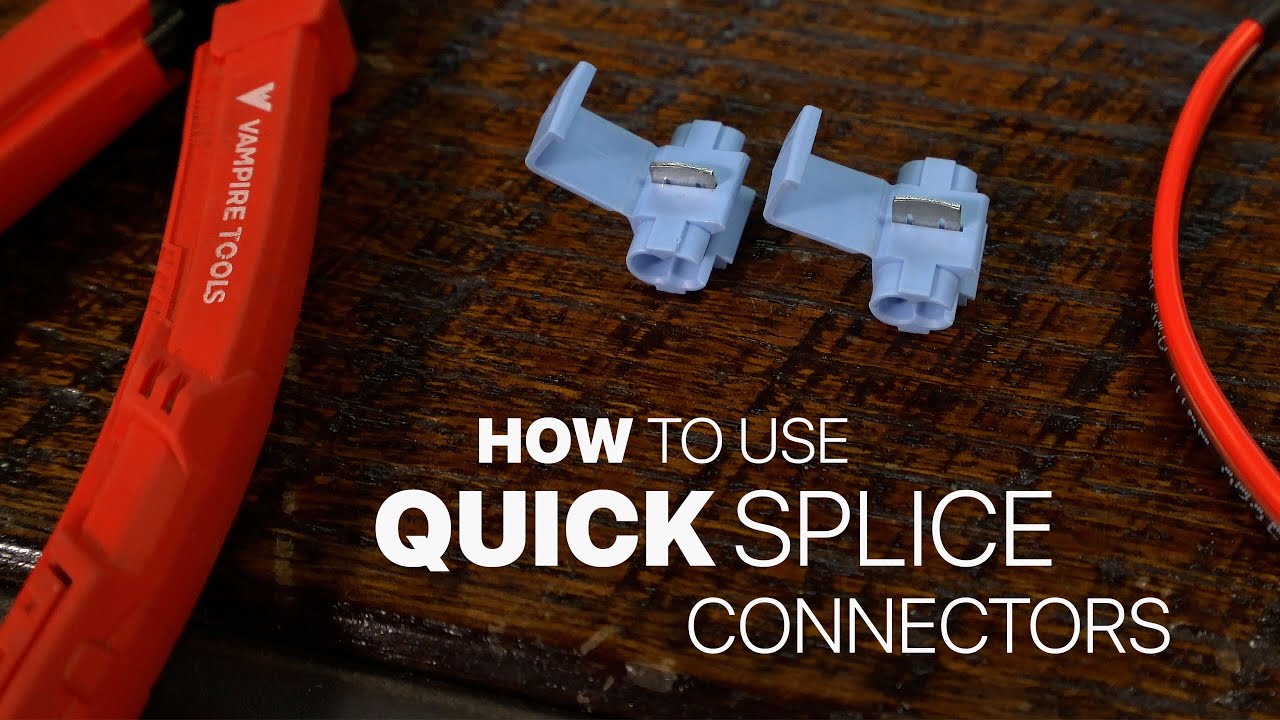
How To Use Quick Splice Connectors Tap Into Your Vehicle's Main
Frequently Asked Questions (FAQs)
6. Question
Answer: Nope, definitely not recommended. Once a crimp connector has been used, it's been deformed to create a specific connection. Reusing it could lead to a weak or unreliable connection, and that's just asking for trouble. Always use a fresh connector for each splice.
7. Question
Answer: Using the wrong size connector is a recipe for disaster. If the connector is too small, the wires won't fit properly, and you won't be able to make a secure connection. If the connector is too large, the wires will be loose, and the connection will be unreliable. Always choose the right size connector for the wire gauge you're working with.
8. Question
Answer: Generally, no. Properly crimped connections are designed to be secure and reliable without soldering. However, some people prefer to solder the connections for added security, especially in high-vibration environments. If you do choose to solder, make sure you do it properly and use a high-quality solder.
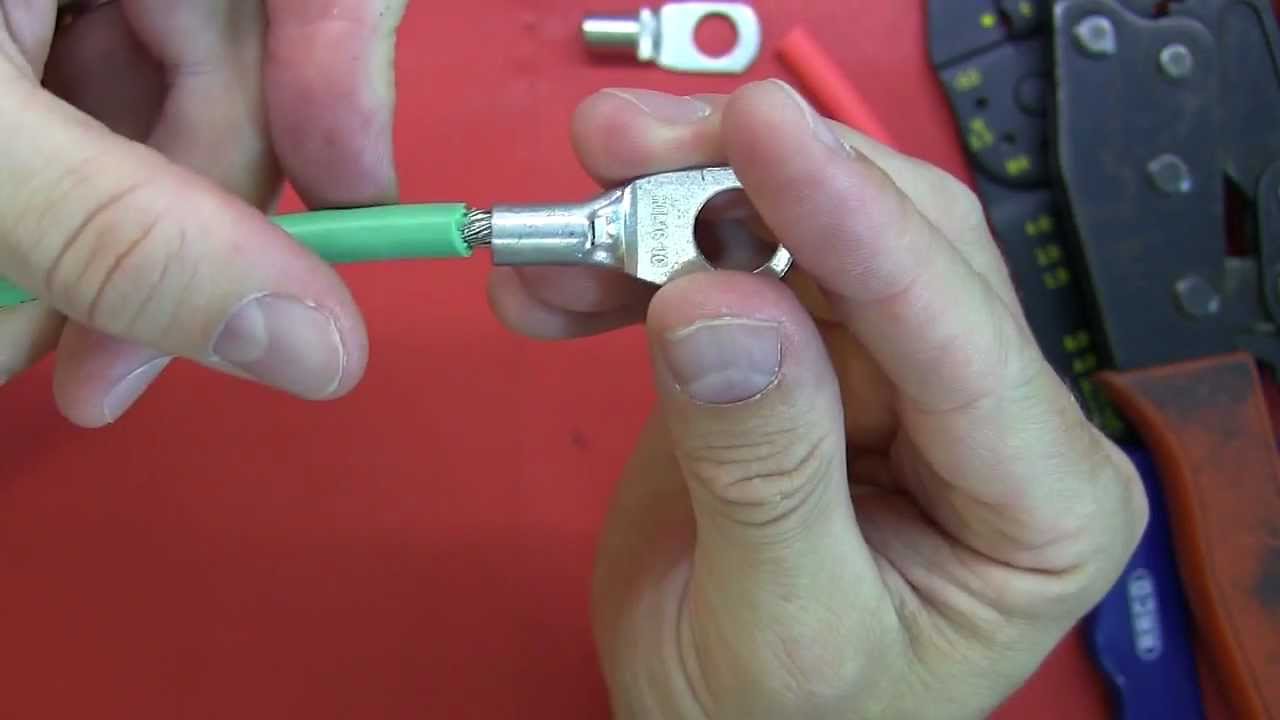

The Lineman's Splice How To Make Reliable Electrical Connections In

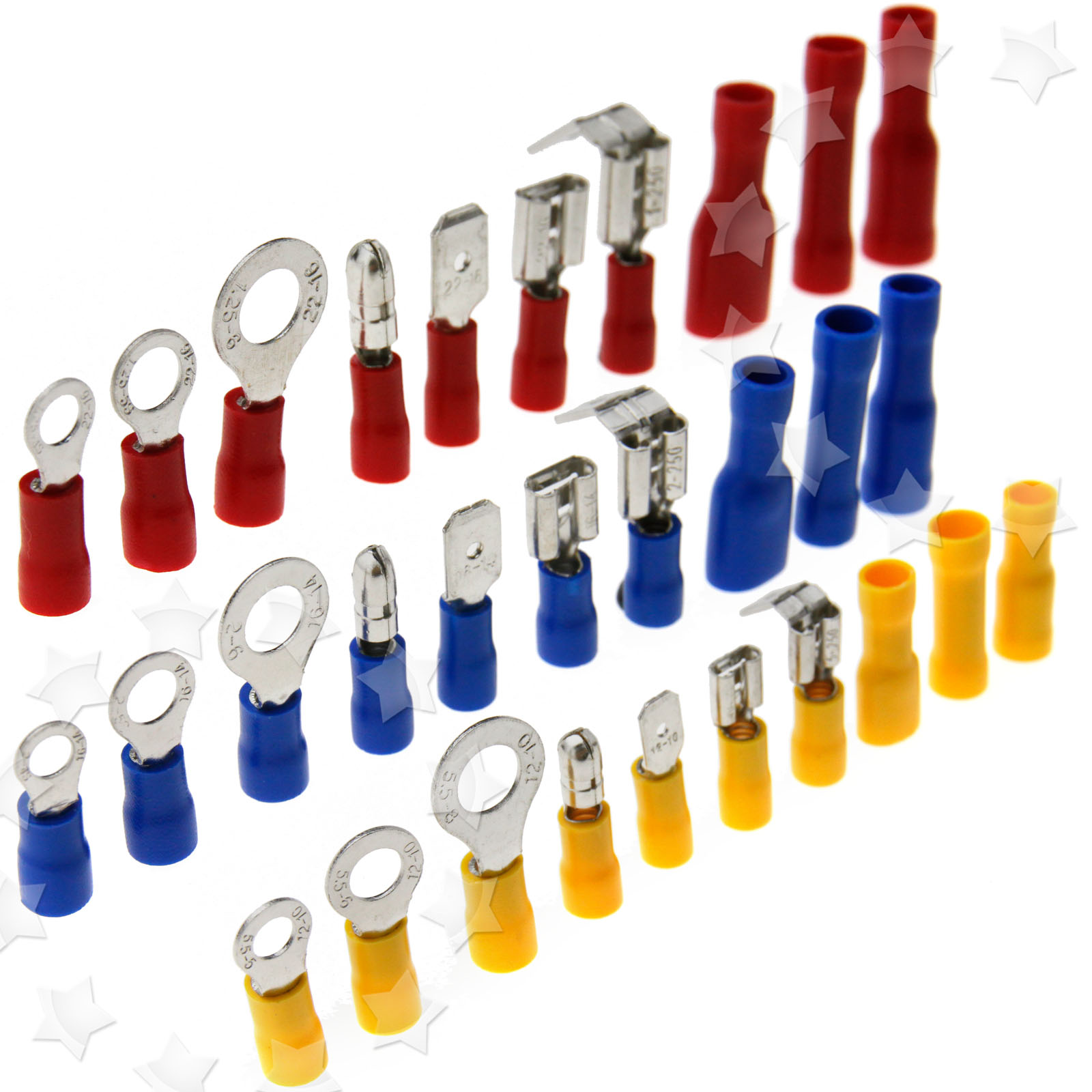